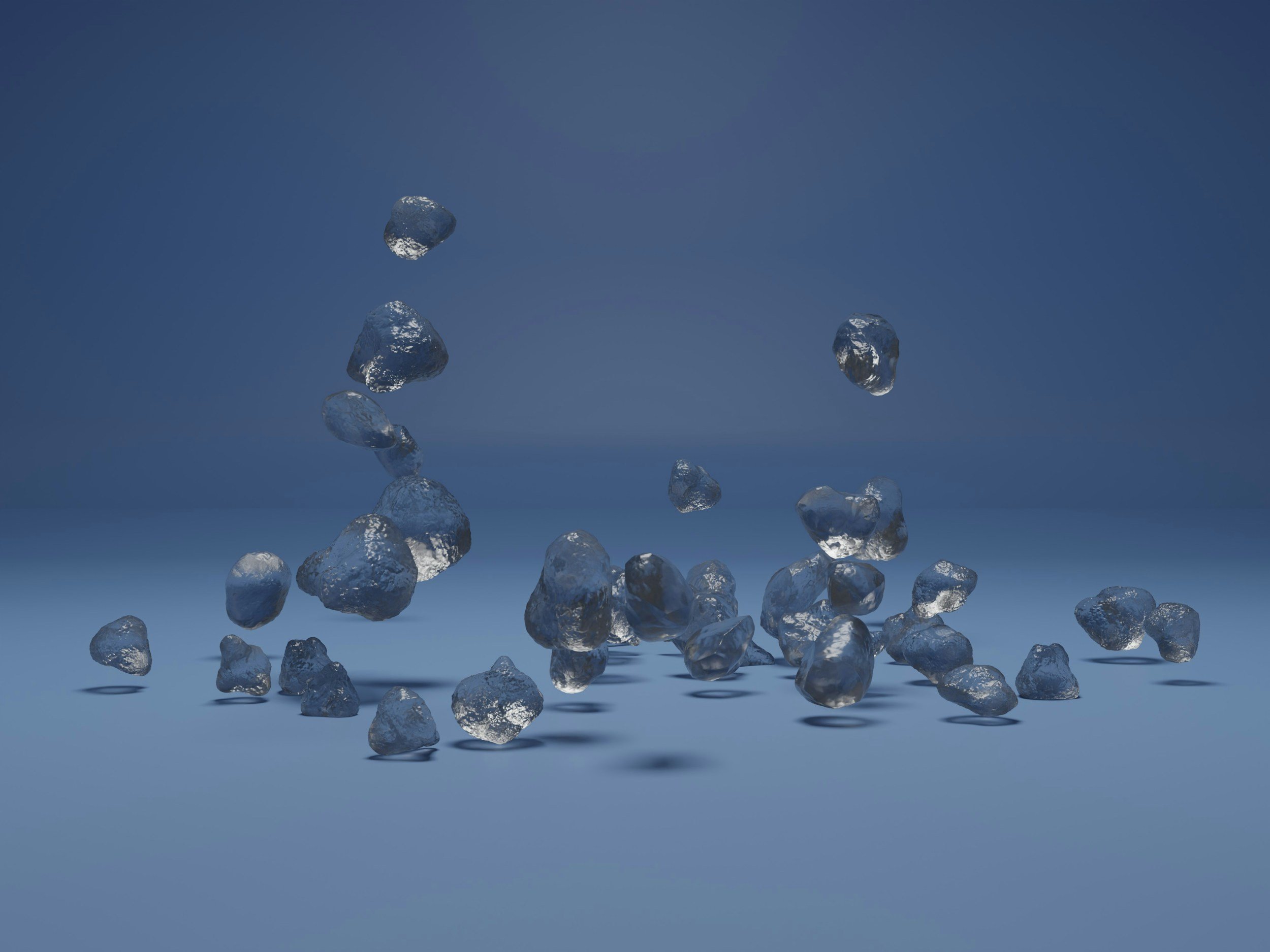
Sintering: Crafting Exceptional Mineral Surfaces for Your Home
Sintering, while cutting-edge, is rooted in ancient practices. Egyptians and Greeks used it for pottery and metalwork, proving its lasting power. Today, we've perfected it to create stunning, durable surfaces: sintered stone, ultracompact options (like Dekton), and porcelain slabs.
Sinterization Process: How Mineral Surfaces are Made:
Three Key Stages
-
Compacting Mineral Powders
In the first step, mineral powders are tightly packed together under immense pressure. This forms the base of sintered stone, ultracompact surfaces, and porcelain slabs, known for their strength and durability.
-
Heating for Particle Fusion
As heat is applied, particles fuse together in a process called necking, where the surface area reduces, and the material becomes solid. This fusion is what gives mineral surfaces their renowned resilience and long-lasting durability.
-
Shrinking Pores for a Solid Finish
During the final phase, pores between particles shrink, creating a non-porous surface. This ensures that mineral surfaces resist stains, moisture, and daily wear, making them perfect for both commercial and residential projects.
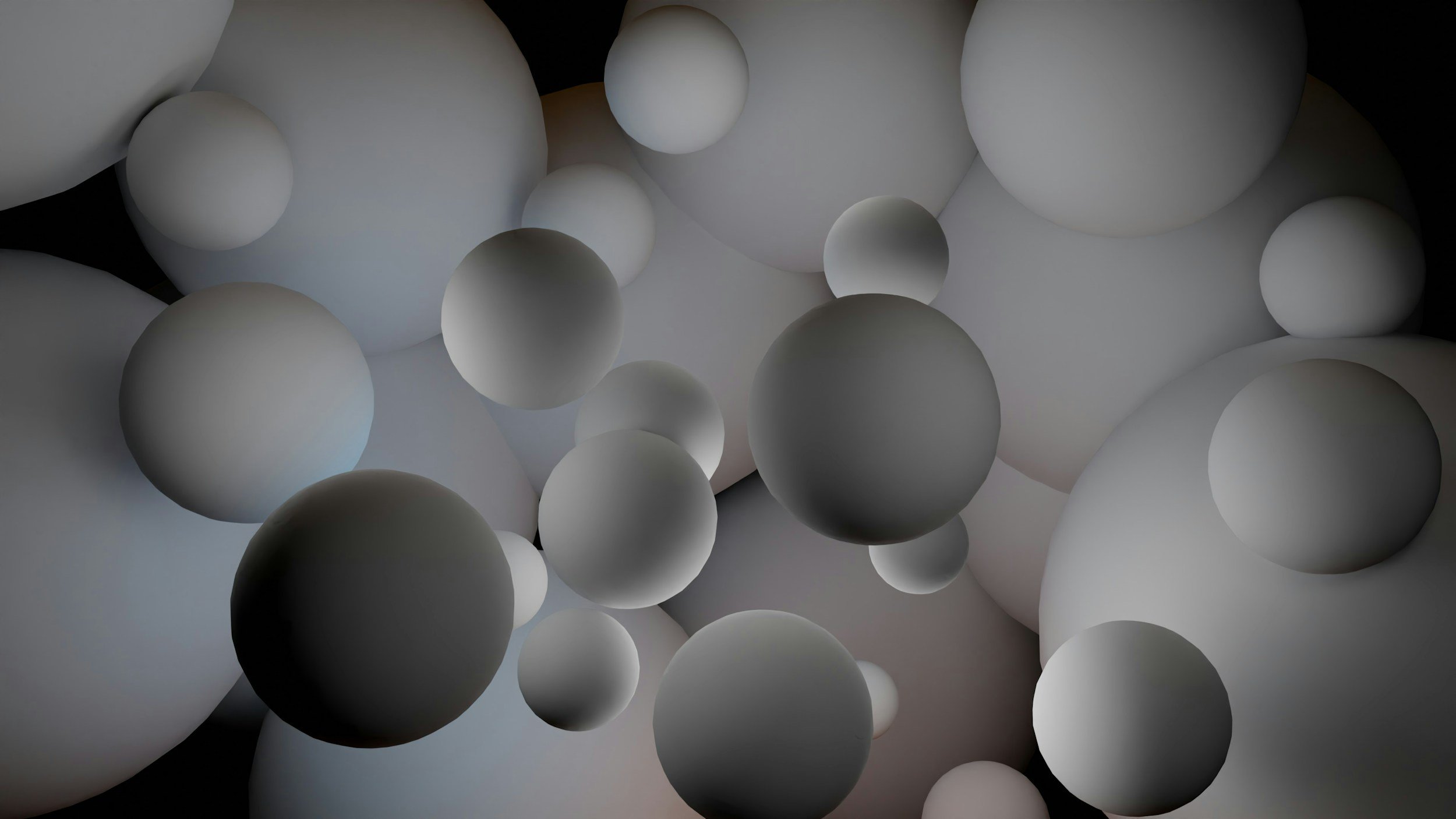
Why the Sintering Process Matters for Mineral Surfaces?
By controlling temperature and time during the sinterization process, manufacturers can create mineral surfaces with different properties. This process is vital in crafting materials like sintered stone, ultracompact surfaces such as Dekton, and porcelain slabs, all of which are renowned for their durability, strength, and design versatility.
The Power of Pressure in the Sinterization Process
The sintering process for creating high-quality mineral surfaces like sintered stone, ultracompact surfaces, and porcelain slabs involves not just intense heat, but also immense pressure. This step is crucial for achieving the superior strength and durability these surfaces are known for.
Understanding the Role of Pressure
To grasp the scale of pressure used in sintering, imagine the weight of a multi-story skyscraper. The Burj Khalifa, one of the tallest buildings in the world, weighs around 500,000 tons. This is comparable to the force applied during the sinterization process, where raw materials are compressed to form solid slabs. Without this pressure, the final product may lack the same level of durability and density that defines high-performance mineral surfaces.
Mineral Surfaces
Mineral Surfaces
Sintering with Pressure vs. Without
Not all surfaces go through this pressurized sintering process. Materials that aren't subjected to this force can have increased porosity and reduced strength, impacting their long-term performance. In contrast, products that Lais Luz works with, which undergo pressurized sintering, offer superior resistance to wear, water, and staining, making them ideal for heavy-duty applications.
“Think of baking a cake: ingredients combine under heat, transforming into something new. Sintering is similar. We press mineral particles together, heat them intensely, and they bond without melting, creating a rock-solid surface.”
Benefits of Surfaces Crafted with Advanced Pressurized Sintering Technology and Premium Ingredients
-
Unmatched Durability
The combination of intense pressure and carefully selected, high-quality minerals results in surfaces with exceptional strength and density. They withstand heavy use, scratches, and impacts, ensuring long-lasting beauty and performance.
-
Hygienic
The absence of pores also prevents bacteria growth, making sintered surfaces a hygienic choice for kitchens, bathrooms, and other areas where cleanliness is paramount.
-
Stain & Moisture Proof
The non-porous nature of sintered surfaces, achieved through high-pressure compaction, makes them impervious to liquids and spills. This means easy cleaning and peace of mind, knowing your surfaces are protected from unsightly stains.
-
Heat & UV Proof
Sintered surfaces are both heat and UV proof. They can withstand the heat of hot pots and pans without damage or discoloration, and their colors remain vibrant even under prolonged sun exposure. This makes them perfect for any space, indoors or out.
-
Bacteria Proof
The non-porous nature of sintered surfaces prevents bacteria from penetrating and multiplying, making them ideal for hygiene-critical environments like hospitals, clinics, and laboratories.
-
Design Versatility
With a vast selection of colors, patterns, and textures, sintered surfaces offer limitless design possibilities to match any style and aesthetic preference.
The Recipe for Success: Ingredients & Time Matter
Just like baking, the minerals, heat, pressure and time create the final product. Each surface type has its own unique "recipe," resulting in different looks and strengths.
Avoid Costly Mistakes: Choose the Right Surface and Fabricator
The exceptional performance of sintered surfaces relies on expert knowledge and precision during fabrication and installation. Mistakes can compromise the surface's integrity, leading to cracks, misalignment, or other costly problems.
Selecting the right surface and a skilled fabricator is crucial for a successful outcome. Whether you're drawn to the modern resilience of Dekton, the timeless elegance of sintered stone, or the versatile beauty of porcelain slabs, partnering with an experienced professional ensures your project looks stunning and performs flawlessly for years to come.
Ready to Find the Perfect Surface for Your Project?
Explore our diverse range of mineral surfaces crafted through the art of sinterization.
Contact us today to discover the right material that matches your vision and requirements.
We'll help you create a space that's not only beautiful but also built to last.